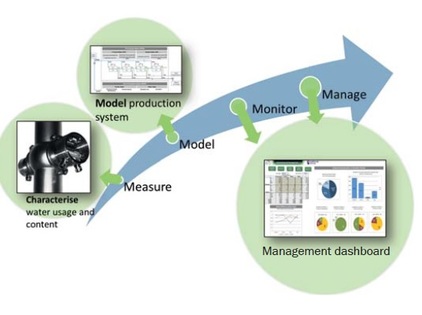
The true cost of water to manufacturers can be up to three times the supply and effluent charges. In addition water shortages, lack of water treatment capacity and ever changing legislation are business risks. In mitigation forward thinking companies have implemented water management policies, but long term sustainable reductions of water consumption in manufacturing can only be achieved through understanding and addressing water use by individual process steps.
The Centre for SMART iis developing a set of flexible, non-invasive water analysis instrumentation to monitor inplant effluent flows across various process steps. The data obtained will be used in a Water Management Framework to identify hotspots for process or product redesign to improve water sustainability.
Methodology
The current water sustainability initiatives in industry are focused on pre- or post-manufacturing measures such as rainwater harvesting or improved effluent treatment. Instead the Centre for SMART is applying its 4M approach (Measure, Model, Monitor and Manage) to assist manufacturing industry to identify and prioritise process-related water reduction opportunities.
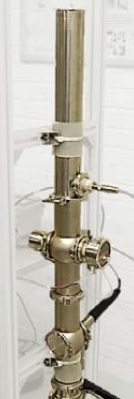
In this approach, the water flow among individual production processes is measured, modelled and monitored to provide transparency and insight into waster usage and effluent generation within a production facility. A set of instrumentation referred to as MASK (Multi- Analyte Sensor Kit) has been developed, capable of providing real time water content data at the unit process level.
The capabilities of the MASK are being characterised and validated using water samples from the food manufacturing industry and validated against standard laboratory based analytical techniques. Data from the MASK will be used to support effective management of water flows within a manufacturing plant and identification of the most sustainable and cost efficient water saving measures.